Molecular Filtration
May 19, 2025
History
The first documented use of activated carbon (known as charcoal) can be traced back to around 3750 B.C. when it was first used by the Egyptians for smelting ores to create bronze. By 1500 B.C. the Egyptians had expanded its use to healing intestinal ailments, absorbing unpleasant odors, and for writing on papyrus. By 400 B.C., the Ancient Hindus and Phoenicians recognized the antiseptic properties of activated charcoal and began using it to purify their water.
Between 400 B.C. and the 1800s, activated charcoal was used to remove odors from wounds, preserve water during ocean voyages, and to treat battle wounds by the military by removing toxins.
The earliest use of activated carbon for gas-phase contaminant removal dates to 1854, when a Scottish chemist invented the first mask that utilized activated carbon to remove noxious gases. Wood was originally used as the base material for gas masks since it was good at capturing poisonous gases when converted to activated carbon. By 1918, it was determined that shells and nuts converted to activated carbon performed even better than wood.
Around this same time, activated carbon began to be produced on a large scale and its use spread to decolorization in the chemical and food industries. In the later 1900s, other industries such as corn and sugar refining, gas adsorption, alcoholic beverage production and wastewater treatment plants began to use activated carbon.
Today, activated carbon is available in many different shapes and sizes and its applications are growing every day. For air filtration, the most common types of activated carbon are granular activated carbon (GAC), pelletized activated carbon (PAC), and structured activated carbon. In addition, other substrates such as alumina and zeolite are used in lieu of activated carbon due to their tremendous pore structures. The most common applications of these different media types include corrosion control, odor control, and protection from toxic gases.
What are Gaseous Contaminants?
Gaseous contaminants are undesirable airborne molecules mixed with the normal molecular oxygen and nitrogen in the atmosphere. Because of their molecular size, in the sub-nano range, they are not visible. Also not visible, but present in the air, is desirable molecular water, which is referred to as humidity. Some common offensive undesirable gaseous contaminants are hydrogen sulfide, the rotten egg smell, or skatole, the dirty diaper smell. Many gases that evolve from combustion are contaminants, such as carbon monoxide, oxides of nitrogen, oxides of sulfur, and polyaromatic hydrocarbons.

Size – Gaseous and Particulate Contaminants
The graphic in Figure 1 illustrates the relative size differences of airborne contaminants. Some particulate contaminants, such as viruses and bacteria, although not visible, have a mass size large enough to be filtered with specialized particulate filters. Gaseous
contaminants can only be effectively removed using molecular gas-phase filtration technologies.
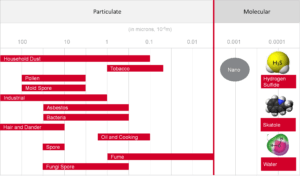
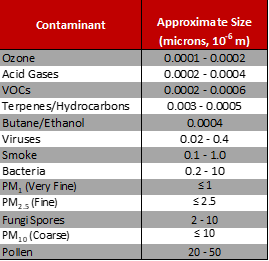
Figure 1
Types and Sources of Gaseous Contaminants
Gaseous contaminants are generally classified as Odorous, Corrosive, or Harmful/Toxic. Examples of their sources are shown in Figure 2.
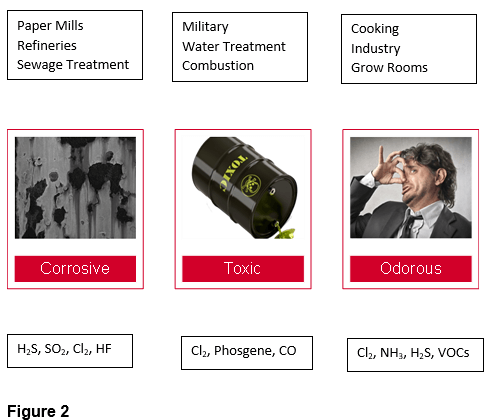
Often, contaminants can be classified in more than one category. One example of this is hydrogen sulfide (H2S) which is both corrosive and odorous.
Control of Gaseous Contaminants
There are various ways to control gas-phase contaminants. One method is source control wherein the source of the contaminant(s) is relocated or eliminated. A second technique is ventilation where large amounts of fresh air are added to the contaminated air to dilute the contaminants. Often, neither of these control methodologies will work. In these cases, gas-phase filtration systems must be utilized. A schematic is shown in Figure 3.
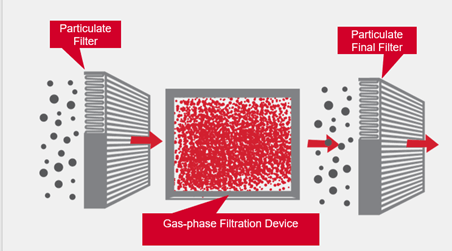
Gas-phase filtration devices are used in combination with particulate filters to remove gaseous contaminants. A particulate filter is always required upstream of the gas-phase filter to ensure that all dirt and dust is removed from the airstream. A particulate, final filter is recommended downstream of the gas-phase filter when the air is going to be recirculated back into an occupied space. The purpose of this particulate filter is to capture any dust that might come off the chemical media in the gas-phase filter. When the air exhausted to atmosphere, there is not a need for a final filter.
Selecting Gas-phase Filtration Devices
Choosing the correct chemical media type and the correct chemical media delivery product is a daunting task. There is a lot of information that must be gathered first such as the contaminants of concern (COC) the concentrations of the COC, the air volume, the desired media life, the space available, and more. A good starting point is completing an application questionnaire like Figure 4 below to document as much of this information as possible.
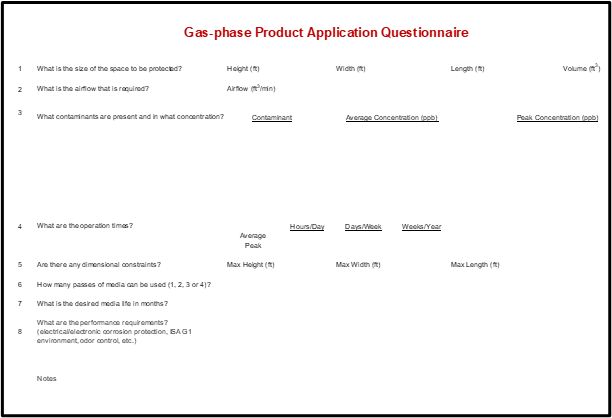
The gathering of the data is the first step in determing the correct media type. In most applications, there is one chemical media type that will work best. There are times, however, when more than one media type will work as well as times when more than one media type is required as part of the solution due to the list of contaminants that need to be removed. To further complicate matters, there are multiple chamical media delivery devices that are available and most of the time, more than one of those devices will work. The amount of space that is available along with number of media types required are the two main factors that will determine which delivery device will best solve the application at hand. Due to this complexity, it is recommended that you reach out to your local filtration specialist to assist you with making the proper selction.
The Minimum Viable Product
The minimum viable product is usually determined by the customer or end user and is defined as the minimum acceptable service life of the filtration device before the chemical media removal capacity is exhausted. Figure 5 below demonstrates how there is usually more than one viable product solution for most gas-phase applications.
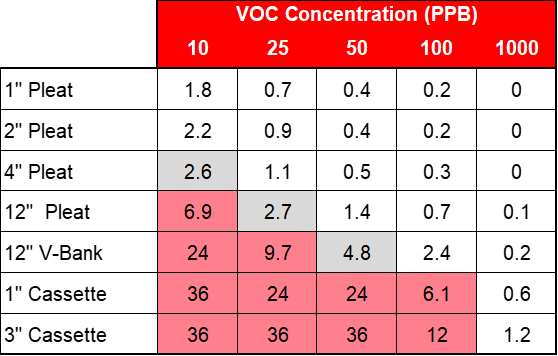
The table shows the expected life in months versus the contaminant challenge for various gas-phase filtration products. The gray boxes show acceptable products for roughly a three-month minimum life and the pink boxes show acceptable products for a six-month minimum life. When evaluating a gas-phase application, it’s important to understand the most important requirements for that application such as first cost, replacement cost, ease of replacement, and space available so the best product value is chosen.
Remaining Life Analysis
When the best chemical media has been determined and the filtration device has been selected, the question of how long this filtration device will last often comes up. The manufacturer of the filtration device should be able to provide an estimate of expected life of the chemical media. To verify that estimate, the remaining life of the chemical media can be tested. Remaining life analysis compares the known, initial capacity to the current capacity of chemical filtration media that is installed in filtration systems. The information obtained from this testing can be used to confirm system performance, determine the media replacement schedule, and to assist with inventory control of replacement media. Replacing media based on testing maximizes the media life, reducing the total cost of system ownership.
Author: Dave Schaaf